Industrial digitalization enables companies to remain competitive and deliver value. It is no longer optional, it has become a necessity for all industries aiming to stay efficient in a global and demanding market.
Digitalization is essential to ensure efficiency, flexibility, quality, and sustainability! Do you believe your company is ready to take the next step? ESI Robotics is here to support you along the way.
The Path to Industry Digitalization: 7 Steps in the Right Direction
1. Assessing the Company’s Current State
Before any investment or change, it is crucial to evaluate the starting point. A technological and organizational audit helps identify:
- Outdated or underperforming systems
- Existing digital systems
- Manual processes with automation potential
- Communication gaps between machines
- The digital skills of your team
This diagnosis forms the basis for building your digital roadmap.
2. Developing a Digital Roadmap – A Clear Vision and Strategy
The digital roadmap is a document that outlines the goals your organisation intends to achieve, highlighting the digital initiatives that will drive the transformation. It connects digital initiatives to both short and long-term business objectives through a clear action plan.
3. Investing in Technological Infrastructure
The foundation of industrial digitalization lies in having a robust infrastructure to support new systems, including:
- Machine and system connectivity (IIoT)
- Integrated management software (ERP, MES, SCADA)
- Platforms for data collection and analysis
- Cybersecurity systems
4. Training and Involving Teams
Digital transformation demands new skills. Training employees and involving them from the beginning is crucial for success. It is essential to encourage teams to see technology as an ally, not a threat.
5. Testing Solutions through Pilot Projects
Choosing pilot projects allows you to test solutions on a smaller scale, measure results, and refine strategies. Common examples include:
- Digitalising a specific production process
- Introducing smart sensors to a production line
- Implementing real-time monitoring dashboards
This approach reduces risks and facilitates team adoption.
6. Connecting and Communicating Data and Equipment
Data collection only becomes valuable when systems are integrated and information is analysed in real time. Industrial digitalization requires a coherent technological architecture where different platforms communicate automatically.
7. Monitoring and Continuous Improvement
Digitalization does not end with the implementation of systems; it is an ongoing process. Key performance indicators (KPIs) must be defined and monitored regularly to assess the impact of changes and identify new opportunities for optimization.
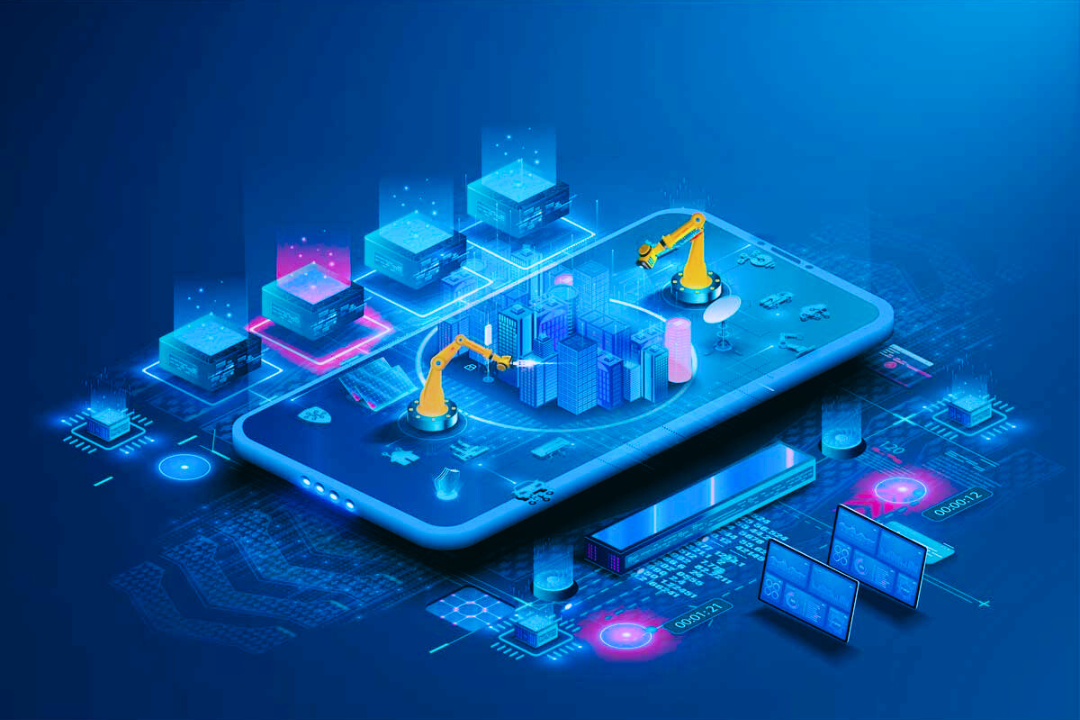
Industrial digitalization represents a strategic leap that can radically transform how companies operate. Preparing for this new reality requires proper planning, the right people, and a future-oriented vision.
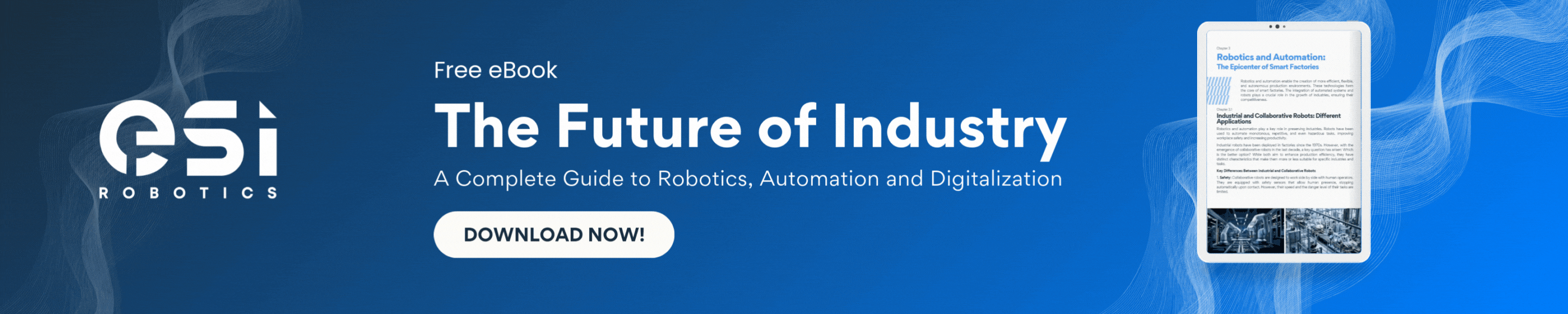