Predictive Maintenance is the key to anticipating failures. Among the various innovations emerging from Industry 4.0, this type of maintenance stands out as one of the most important technologies for optimizing processes and reducing operating costs. But what are the main advantages of predictive maintenance? What distinguishes it from other types of maintenance? How can it be implemented on the shop floor? Read on to find out!
What is Predictive Maintenance?
Predictive maintenance is a monitoring and data analysis technique used to identify potential anomalies in the functioning of equipment, making it possible to predict failures before they happen. This technology is based on the data collected to understand trends and thus anticipate errors.
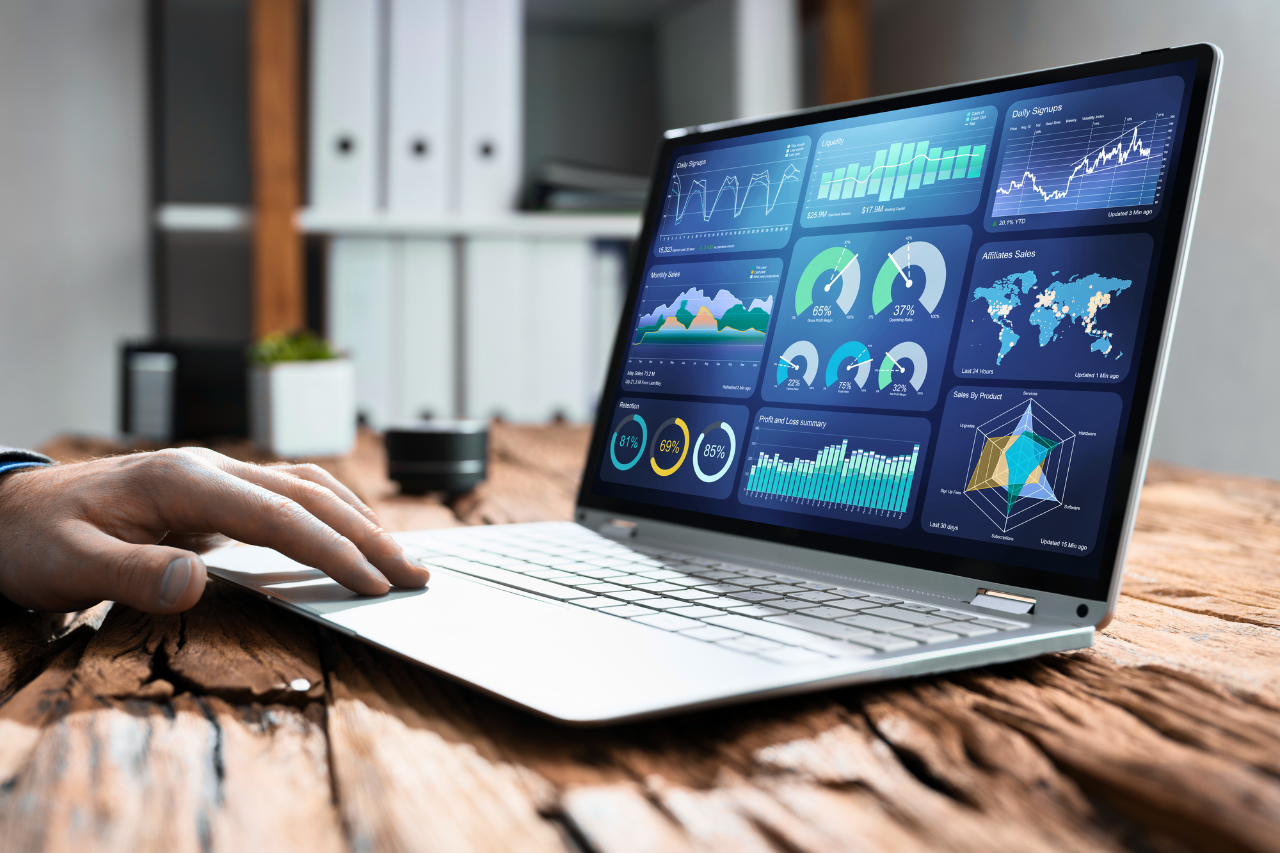
Preventive and Corrective Maintenance - Main Differences
- Corrective Maintenance: Also known as reactive or breakdown maintenance, this is carried out when a fault has already occurred and the damaged equipment needs to be repaired.
- Preventive Maintenance: This involves the periodic inspection of machinery, regardless of whether there is any apparent need for intervention (such as an unusual noise).
The benefits of predictive maintenance
-
1. Cost reduction: Despite the initial investment, predictive maintenance enables a more efficient use of resources, minimizing the need to replace parts and reducing downtime. Companies can thus avoid the high costs associated with unexpected downtime.
-
2. Increased equipment lifespan: By identifying problems before they occur and worsen, predictive maintenance contributes to extending the useful life of equipment. Constant monitoring makes it possible to adjust operations and avoid unnecessary wear and tear. The more knowledge we have about how a piece of equipment works, the easier it is to define good maintenance practices and, consequently, extend its useful life.
-
3. Improved safety: Predicting failures improves safety in the workplace by minimizing the risk of accidents caused by unexpected breakdowns. Predictively monitored equipment is less likely to suffer serious failures, thus protecting workers and the environment. Predictive maintenance can even predict accident trends. In this way, the company can anticipate and implement prevention and safety measures.
-
4. Optimizing Production: Reducing unplanned downtime improves operational efficiency, contributing to a more consistent and predictable manufacturing. This is crucial in Industry 4.0, where interconnectivity and automation are key to competitiveness.
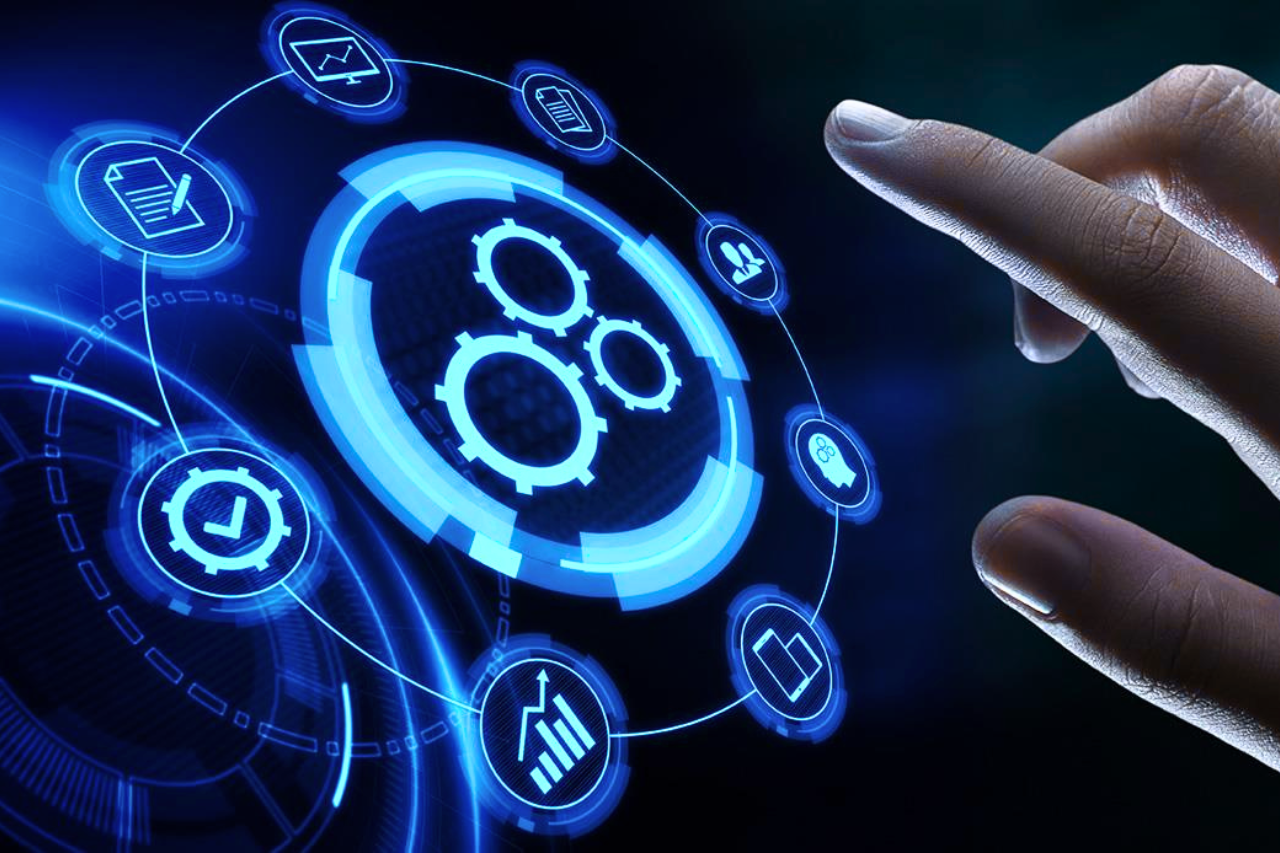
Implementing Predictive Maintenance on the shop floor
Implementing predictive maintenance in Industry 4.0 requires the integration of various technologies, such as IIoT, sensors, which when installed in equipment collect data in real time on various conditions, such as temperature, vibration, pressure and wear; Big Data and Data Analysis; Artificial Intelligence and Machine Learning, which process the data collected, continuously learning and improving maintenance forecasts.
To implement these technologies on the shop floor, it is important to define a management plan. The first step is to identify critical assets, i.e. equipment whose failure can result in major costs and problems for industries. Next, it is crucial to think about failures; an analysis must be made of which are the main types of breakdowns and which should be monitored.
The next step is to find the tools, sensors and software that meet your needs in order to obtain the best fault anticipation diagnosis. Finally, once everything is in place, predictive models need to be developed based on the data collected, which will be tested and validated over time.
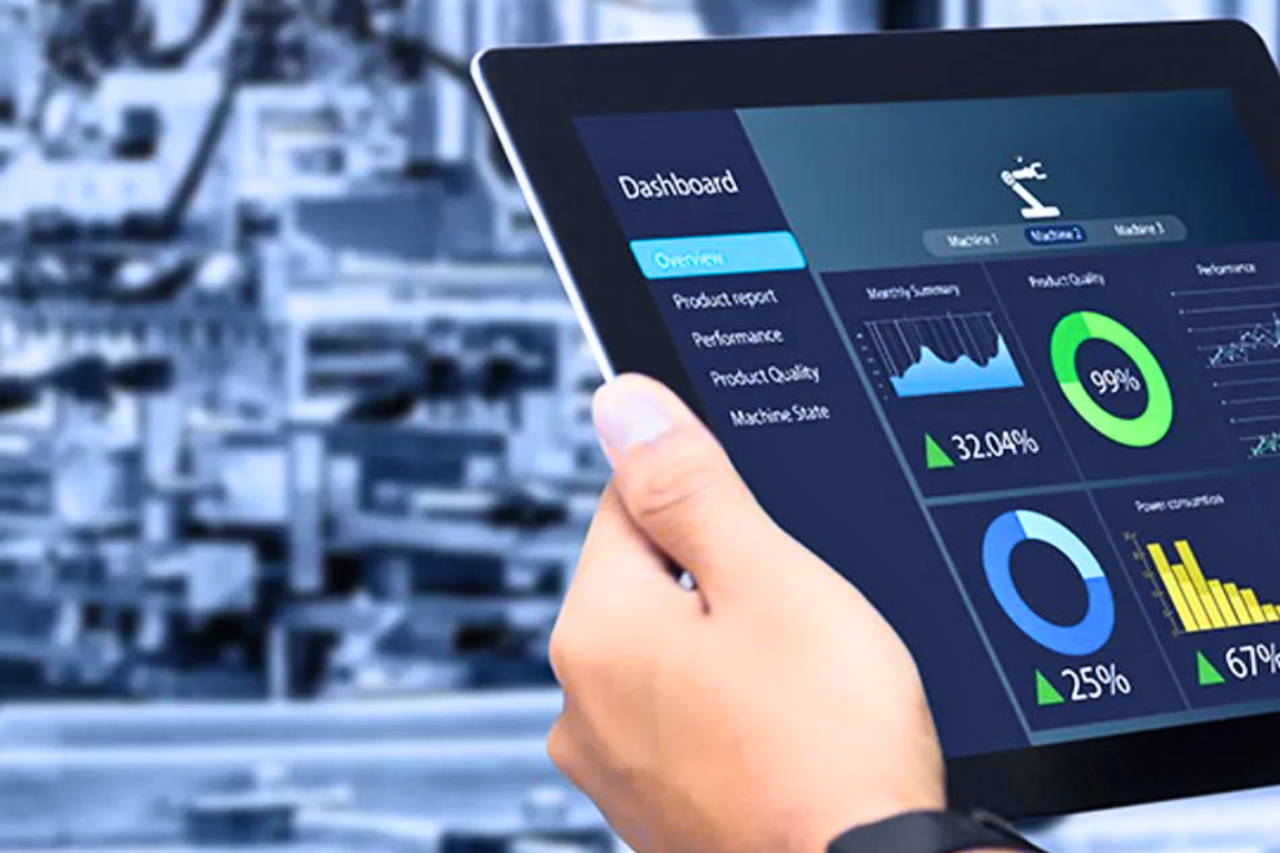
Companies that adopt predictive maintenance practices are better placed to face the challenges of the future and make the most of the opportunities offered by the fourth industrial revolution.
Do you want to implement Predictive Maintenance in your company? Talk to us!
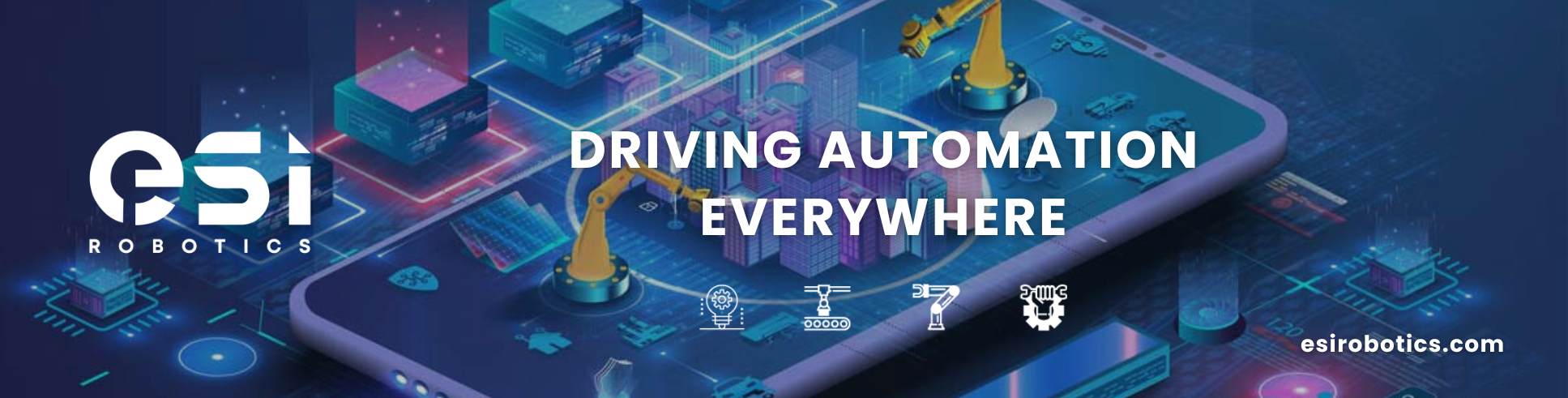