Today we are presenting a case study on one of the most complete solutions we have developed for the rope industry. This production line manages automatically different end-of-line processes. In this article, we highlight not only the benefits that the ESI Robotics solution has brought to this industry, but also the challenges it has faced.
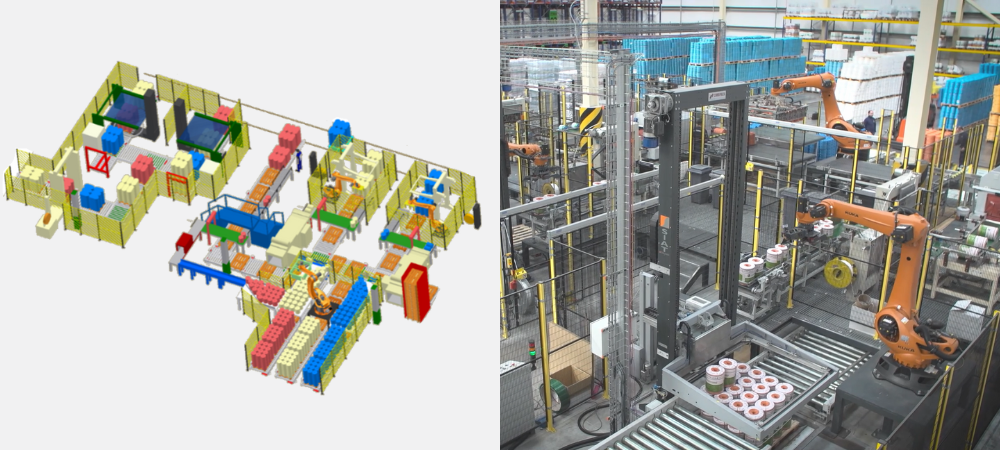
Handling heavy loads is a job that carries health risks for employees. These tasks, when done improperly, can result in injuries and even work accidents.
ESI Robotics' Solution:
To meet the customer's needs, ESI Robotics has developed an automated production line consisting of several stages:
-
- Depalletizing, Transport and Handling: At the first stage of the production line, the products are received on pallets. To handle the reels and continue with the industrial processes, we install industrial robots and conveyors to carry out transportation efficiently;
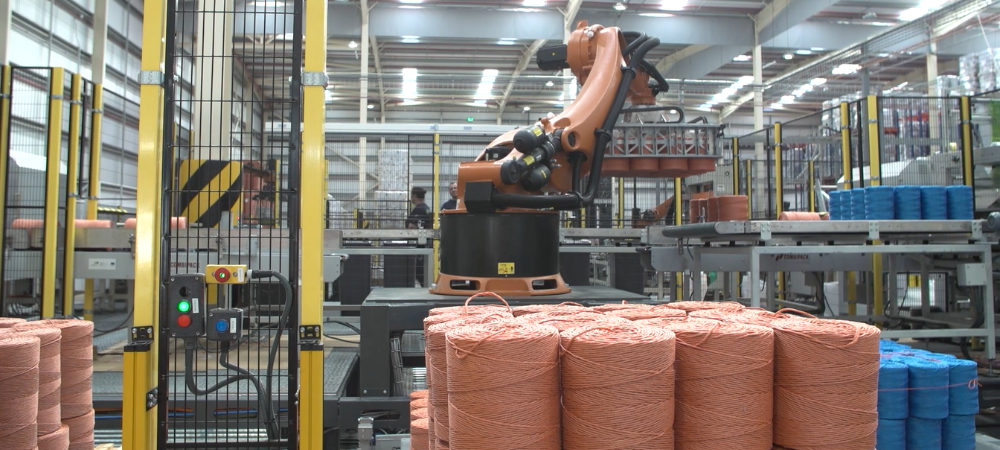
-
- Individual packaging: First, the rope bobbins are individually packaged using automatic machines;
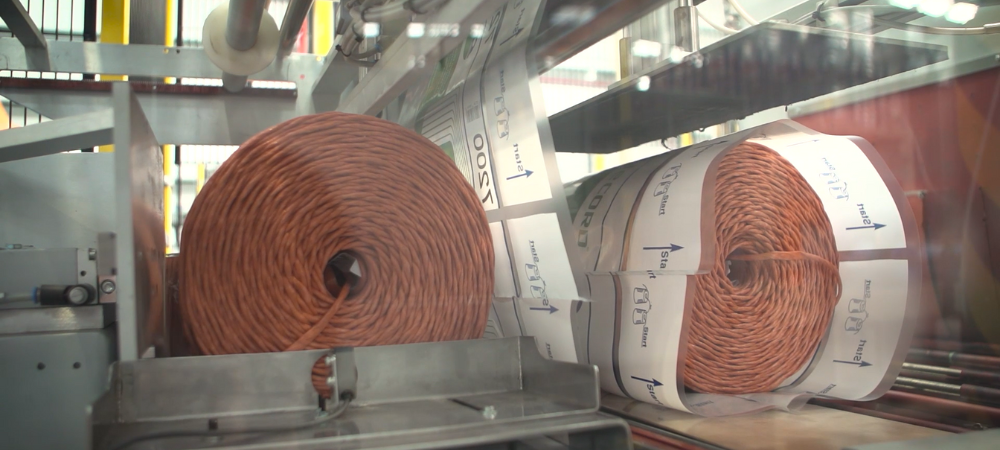
-
- Strapping: Since the bobbins have a cylindrical shape, it was decided to strap the products two by two to ensure stability;
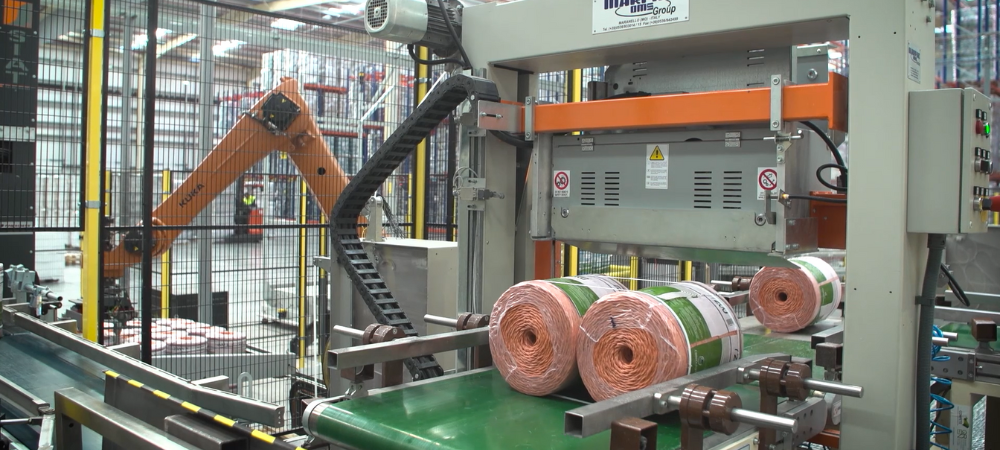
-
-Palletizing and Automatic Transfer: The bobbins of rope are handled and organized on pallets by an industrial robot;
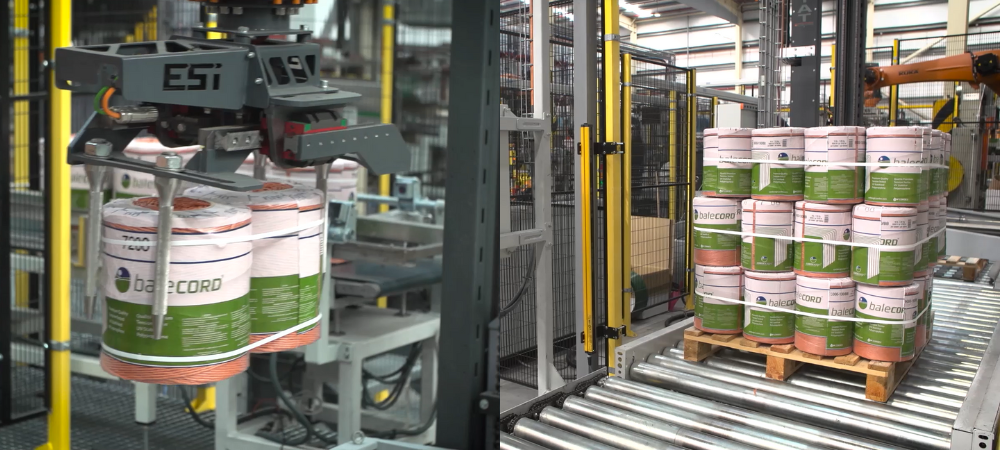
-
- Palletizing with level strapping: When the robot finishes a level of palletizing, a machine straps it so that transport can be carried out safely;
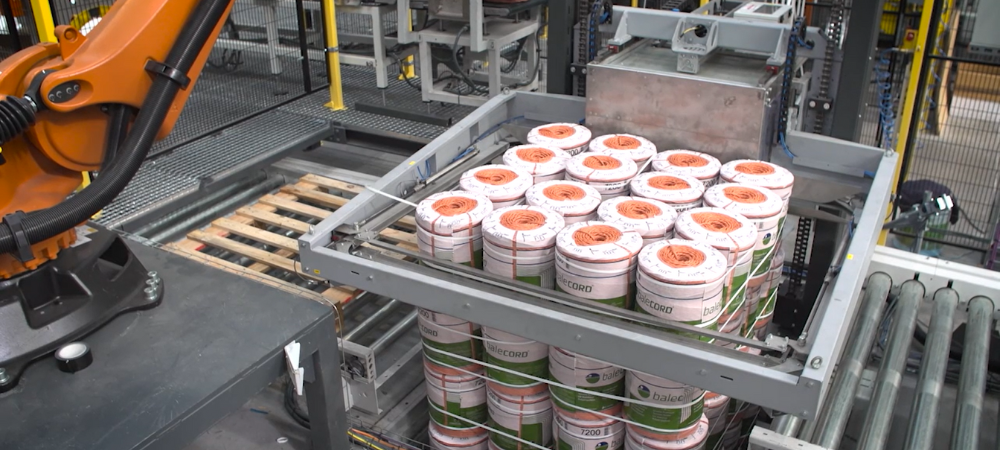
- - Automatic Transfer: To transport the complete pallets to the next step, the line is equipped with an automatic transfer, which collects the pallets from three different stations and delivers them to the next step;
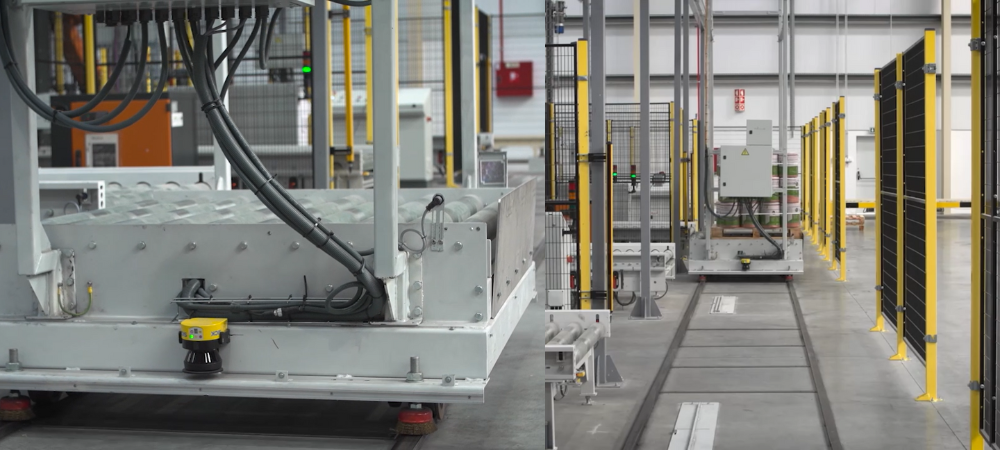
- - Automatic wrapping: Pallets are wrapped to ensure their stability during transportation;
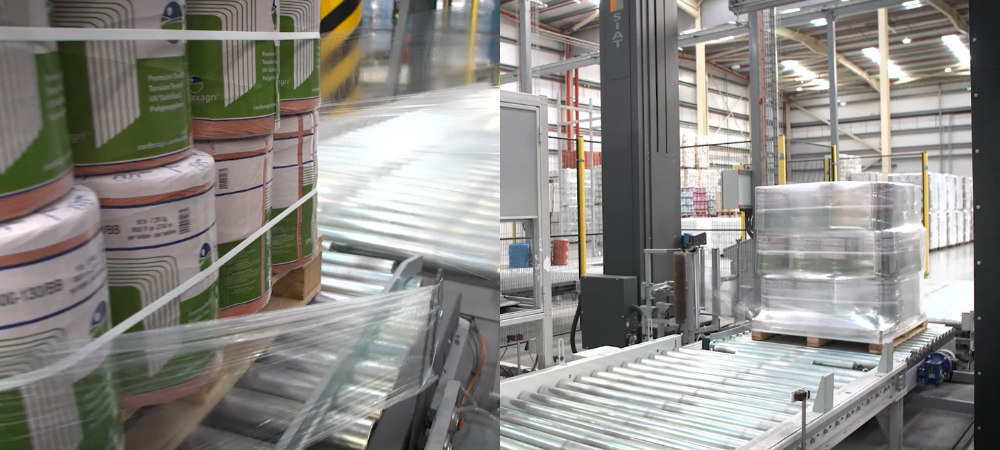
- - Labelling: To optimize stock management, all pallets are labelled at the end of the process;
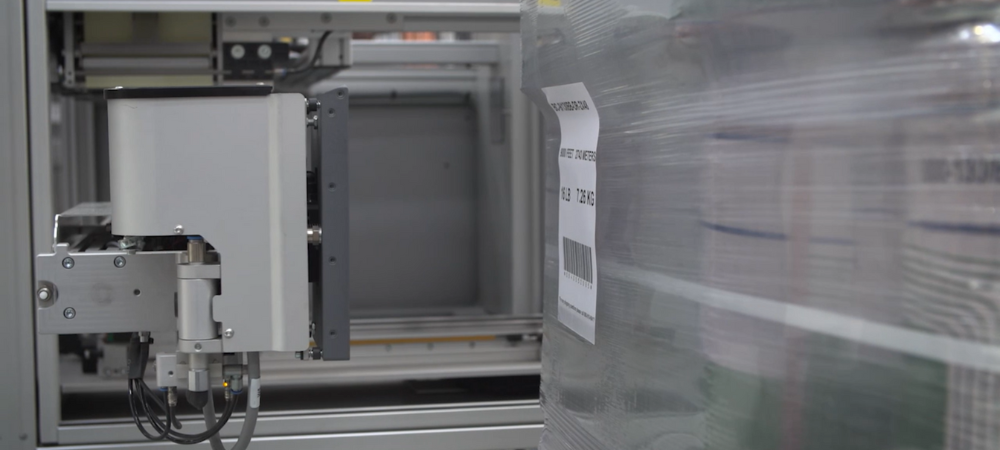
- - Pallet stacking: Finally, pallets are stacked automatically to optimize storage space and transport.
The installation of this fully automatic production line has resulted in a significant increase in productivity and improved worker safety, due to the reduction in manual handling of heavy loads. This case study illustrates how automation can be successfully applied to optimize end-of-line processes.
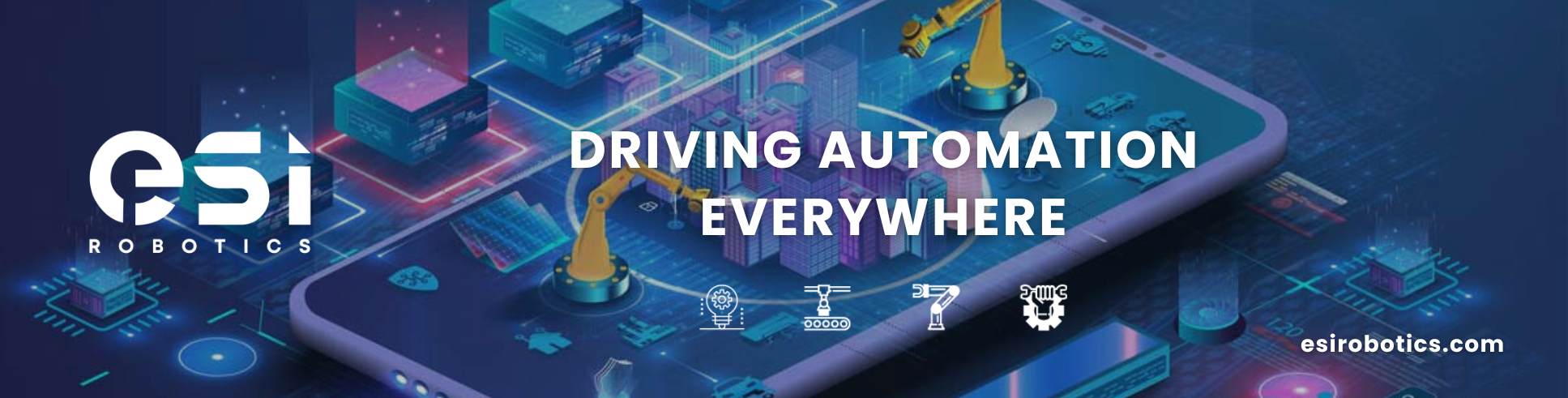