The plastics industry is one of the forces of the global economy, playing a vital role in various sectors, from packaging to the production of components for the automotive sector. As a developing area with a major economic impact, it faces the need to reinvent itself. In this article, we will explore how innovation through industrial automation and robotics can revolutionize this industrial sector. We present three case studies of solutions developed by ESI Robotics for companies looking to optimize their industrial processes.
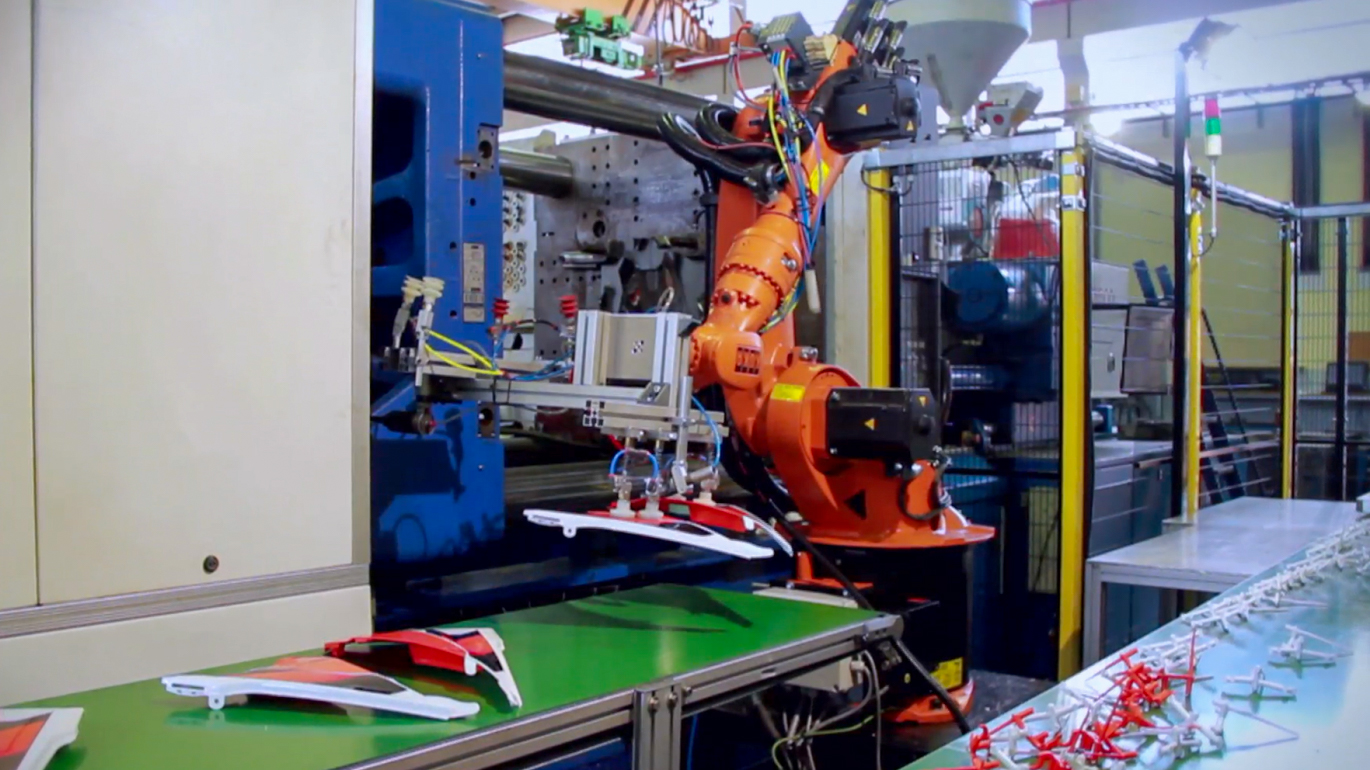
The case studies we present highlight the challenges ESI Robotics has faced, the solutions implemented, and the results achieved. Innovation in this industrial sector is not just about developing new materials, it also involves transforming manufacturing processes.
he use of robots in the plastics industry is becoming increasingly common, as they offer various advantages for production, especially in terms of productivity and the quality of the product. In addition to the obvious advantages, robotics can be applied comprehensively, automating different production processes, from prototyping to transformation processes, including the assembly of plastic components.
Cartesian robots are traditionally the most widely used in this industry. They are usually used to remove injected parts from molds and place them on transport conveyors. ESI Robotics has applied anthropomorphic robots to perform complex technical tasks. Discover three case studies:
GLNPlás - Injection cycle with insertion of 28 metal inserts per cycle
ESI Robotics developed a technically complex solution for the company LNMoldes (now GLN Plas). The challenge was the orderly placement of 28 metal inserts in a mold every injection cycle (70s). The mold had two cavities, in each of which 14 inserts had to be placed with 3 different types of parts (6 + 6 + 2). To make the process more difficult, the customer had no space available on the periphery of the machine. We studied the processes and developed a specific preliminary design for the needs presented. To solve the space problem, they proposed building a structure at a dedicated height (2nd floor).
The solution was divided into 4 distinct phases: Preparation, division, organization and insertion of the metal parts; Distribution and organization of the parts with the correct distances between them (inserts in the final part); Pick and Place of 14 parts simultaneously - Placement of inserts in the mould; Quality control.
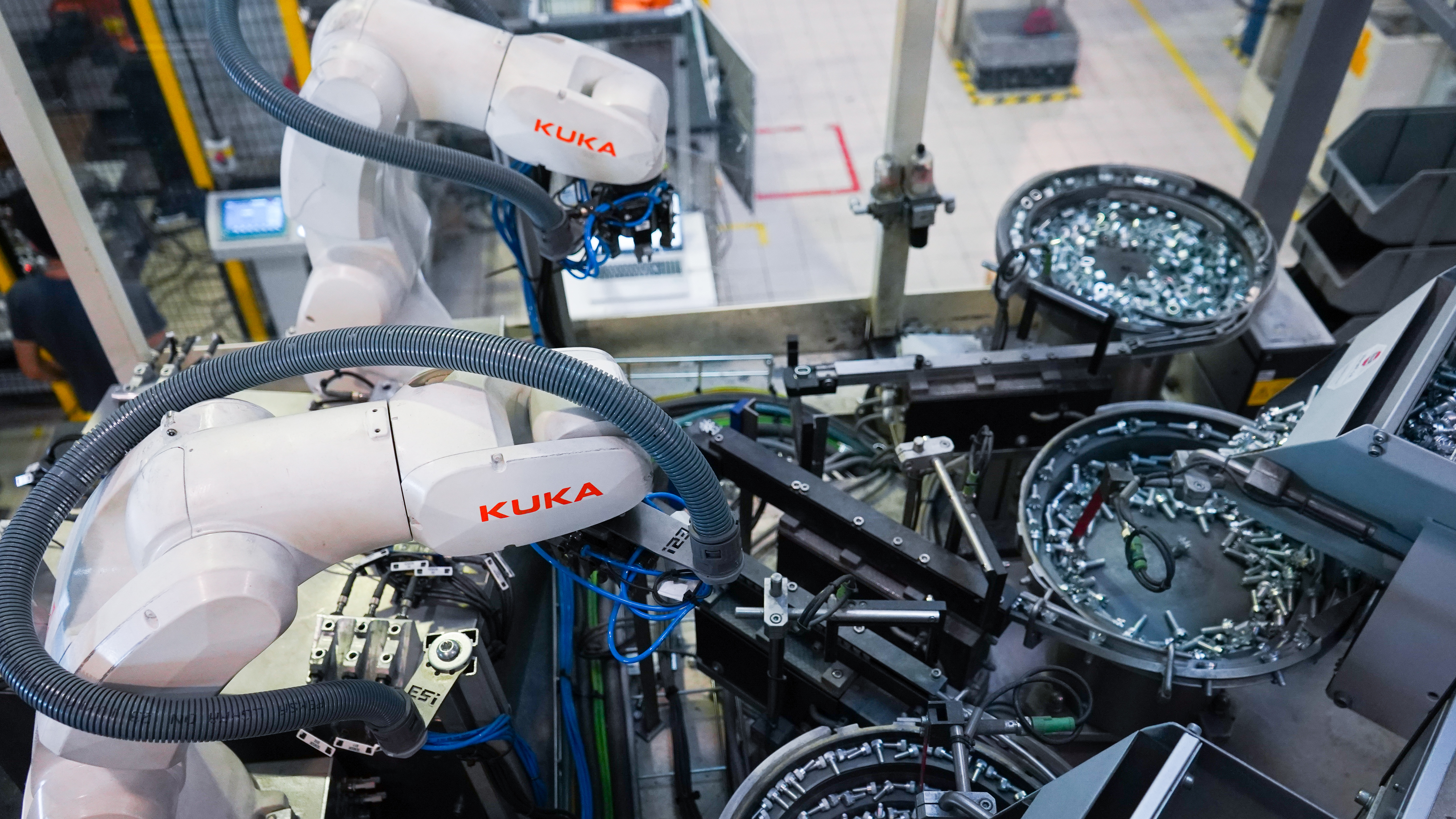
Polisport: Implementation of IPD technology – Inmold plastic decals
ESI Robotics was challenged by Polisport to develop a solution for placing films in injection molds using IPD - inmold plastic decals, a patented technology exclusive to Polisport. After understanding the processes, ESI created a system for storing/dispensing the films and a specific vacuum tool for handling them. They integrated a robot, connected to an injection machine.
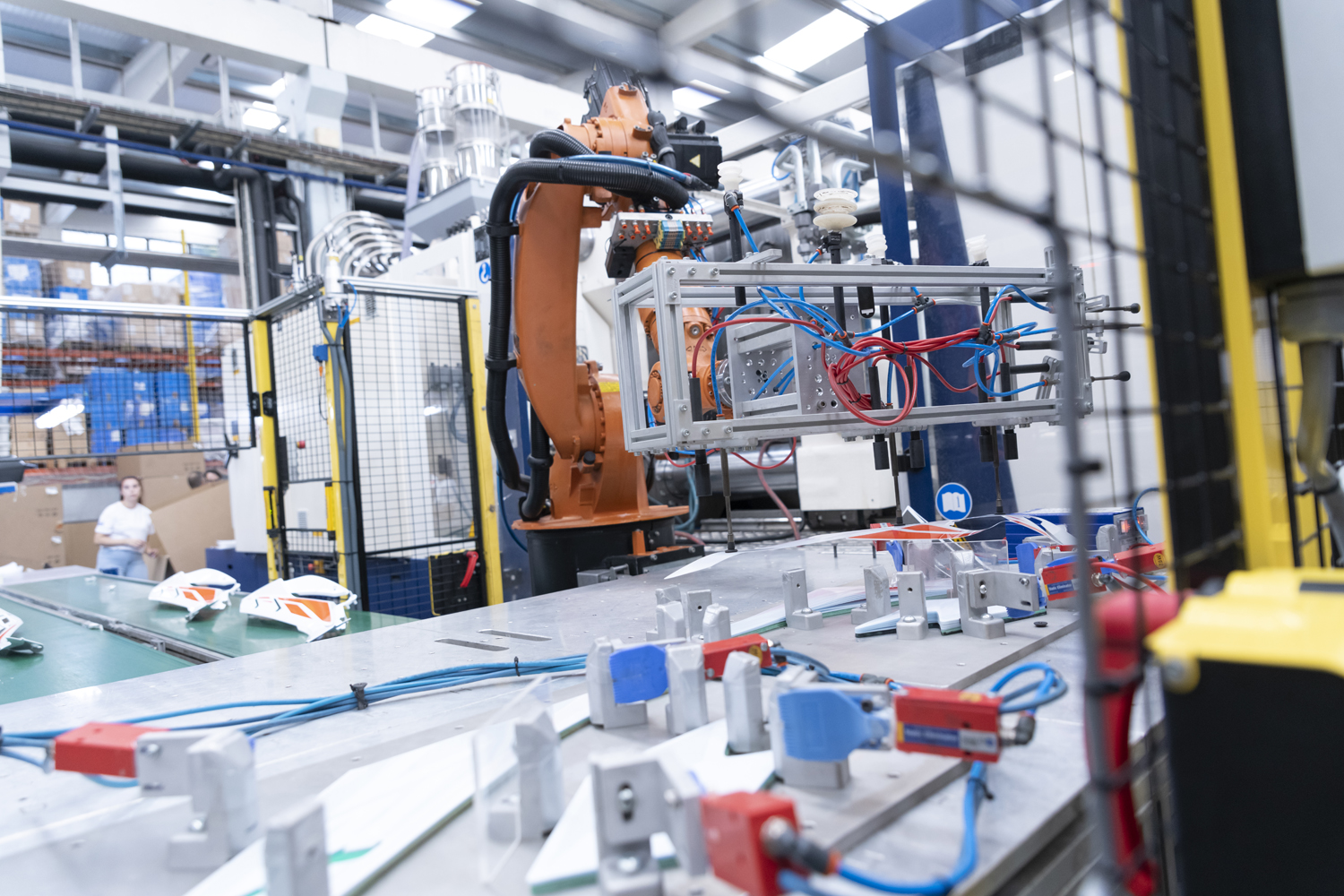
ITP Koozi – Implementation of IML technology – Imprint moulding
Finally, ESI Robotics installed an anthropomorphic robot in the ITP Koozi to work directly with the injection machine, where the IML - Imprint moulding concept was applied. This made it possible to provide the parts with precise graphic images. The robot was also put to good use in die-cutting and label applications.
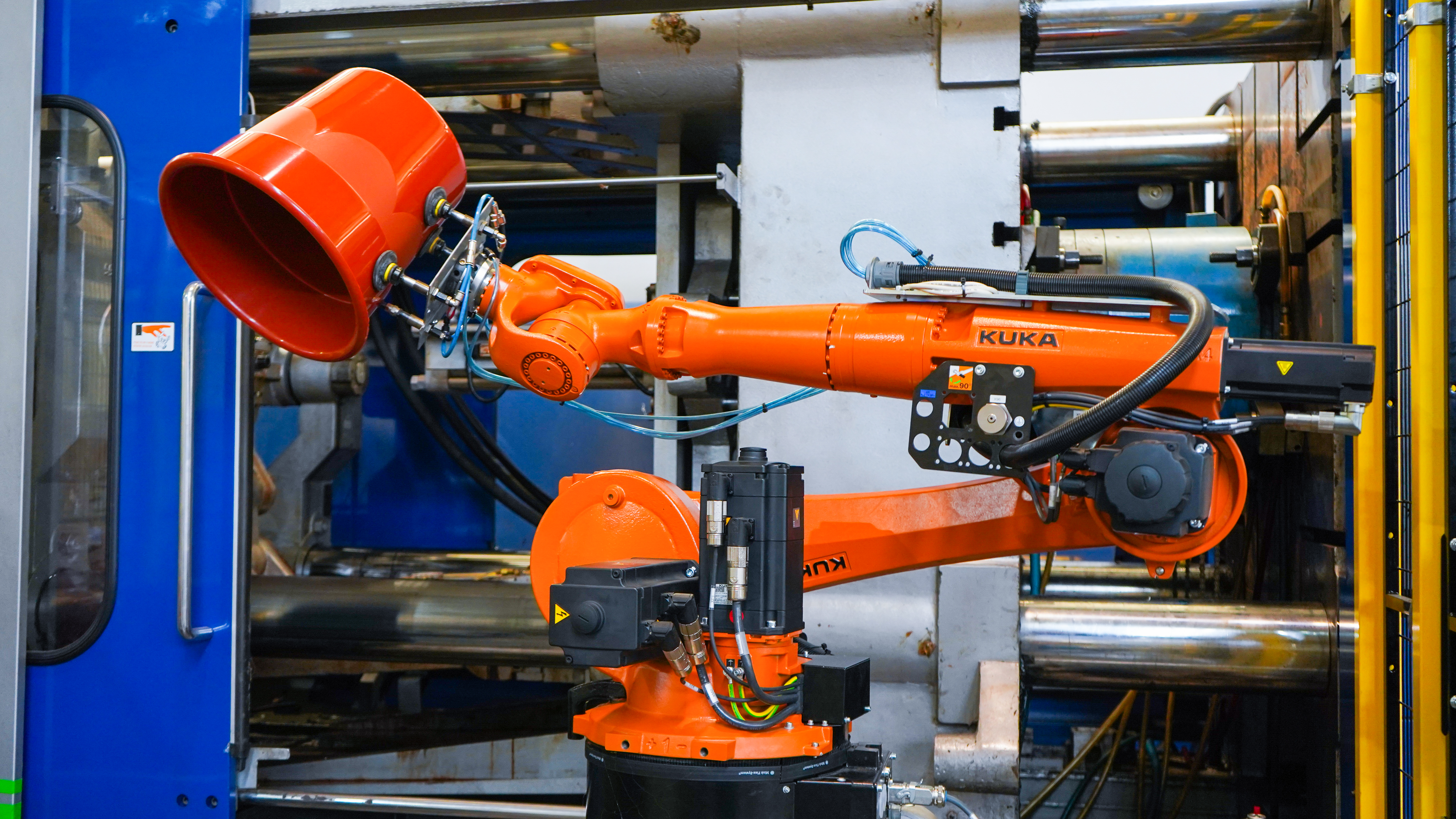
See also: Multi-Process Robotic Cell: Automation for the Plastic Industry
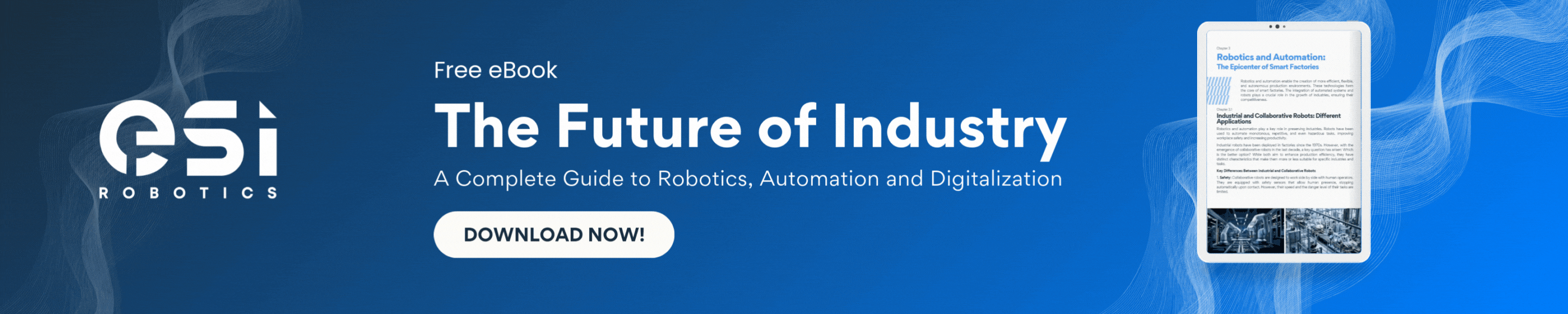