Robotics and automation play a significant role in the preservation of industries. Robots have been used to automate monotonous, repetitive, and dangerous tasks for workers, improving the safety conditions of production processes and increasing the productivity of companies.
Industrial robots have been installed in factories since the 1970s, but with the emergence of collaborative robots, the question has been raised: Which is the best option for your company? Although both aim to improve production, they have distinctive characteristics that can make them more or less suitable for each industry and specific task.
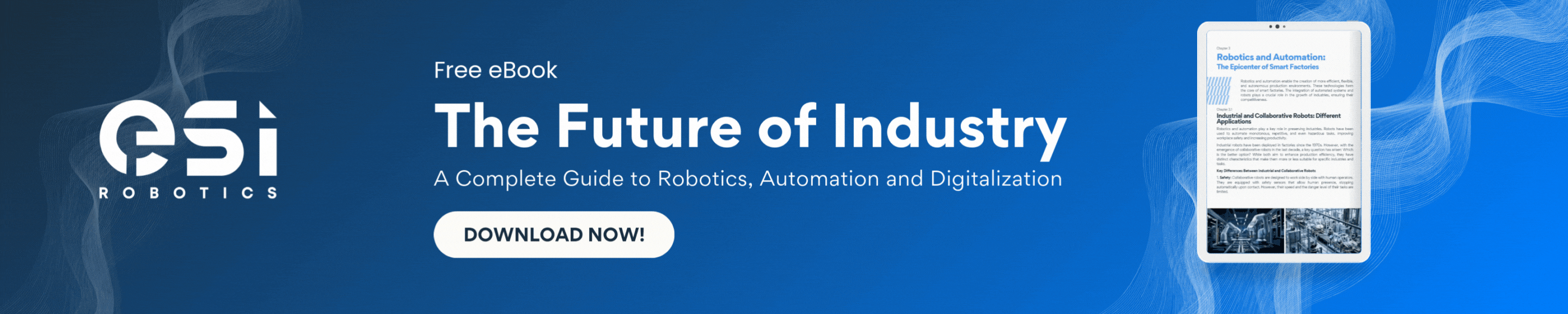
This article will discuss the main differences between industrial and collaborative robots, and how they can maximize efficiency in your industry.
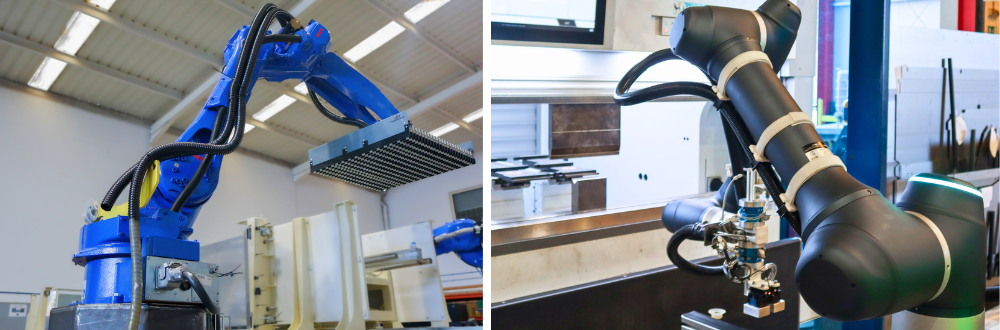
Key differences between industrial and collaborative robots:
1. Safety: In the case of collaborative robots, they have been developed to work side by side with workers. They are equipped with safety sensors that can detect human presence and stop automatically if they encounter anyone. Industrial robots, on the other hand, operate in isolated environments, separated from workers by safety features such as barriers;
2. Precision: Industrial robots can perform repetitive and standardized tasks with high precision and speed. They are often used in assembly tasks, welding, painting, cutting, packaging, and other operations that involve repetitive and precise moves ultimately have greater range and precision than collaborative robots;
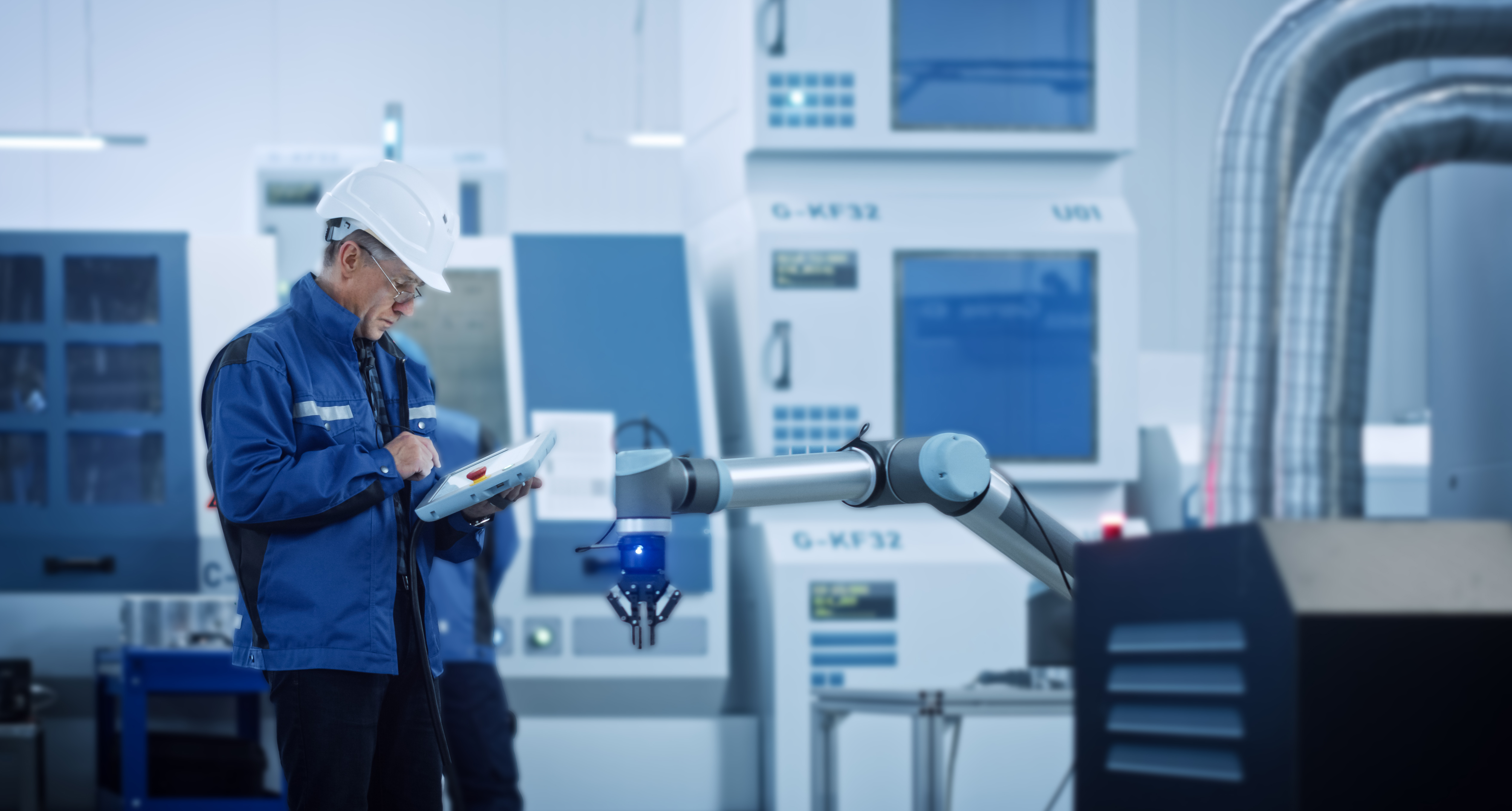
3. Flexibility: Generally, collaborative robots are more flexible, which allows them to be reprogrammed more easily to perform new tasks. In the case of industrial robots, they end up being less adaptable, since they are designed to perform a specific task;
4. Payload: In general, collaborative robots have a smaller payload and a more limited reach than industrial robots;
5. Level of Automation: Industrial robots typically operate in fully automated environments, replacing humans in repetitive and hazardous tasks, and working towards productivity. Collaboratives can work side by side with workers, complementing their work;
6. Cost: in general, collaborative robots are more expensive than industrial robots. The main goal of these robots is that they are cost-efficient, with a focus on productivity and task performance.
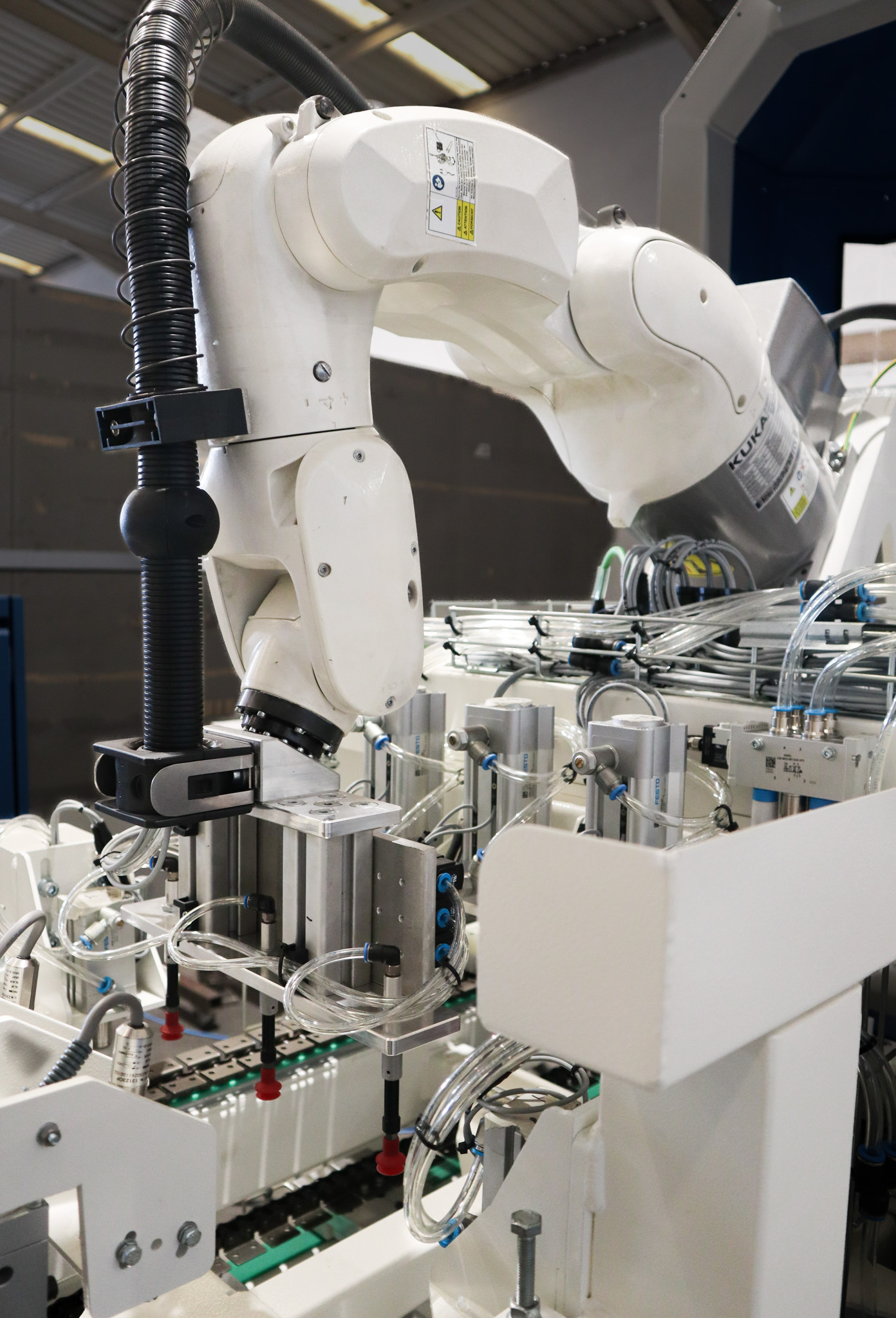
Which is the best choice for each industry?
There is no right answer to choosing between these types of robots. It depends on several factors specific to each industry, the tasks to be performed and the working conditions. In this sense, some points should be taken into consideration and that can help choose the best option:
1. Tasks to be performed: It is important to understand what tasks we want the robot to perform and assess whether they are repetitive and standardized or involve human interaction. For example, if the tasks are highly repetitive and involve predictable movements and no human contact, an industrial robot may be the best option;
2. Work environment: An industrial robot may be more suitable if the shop floor environment is structured and isolated. However, if the industry in question involves shared spaces and human interactions, a collaborative robot may be the safest option;
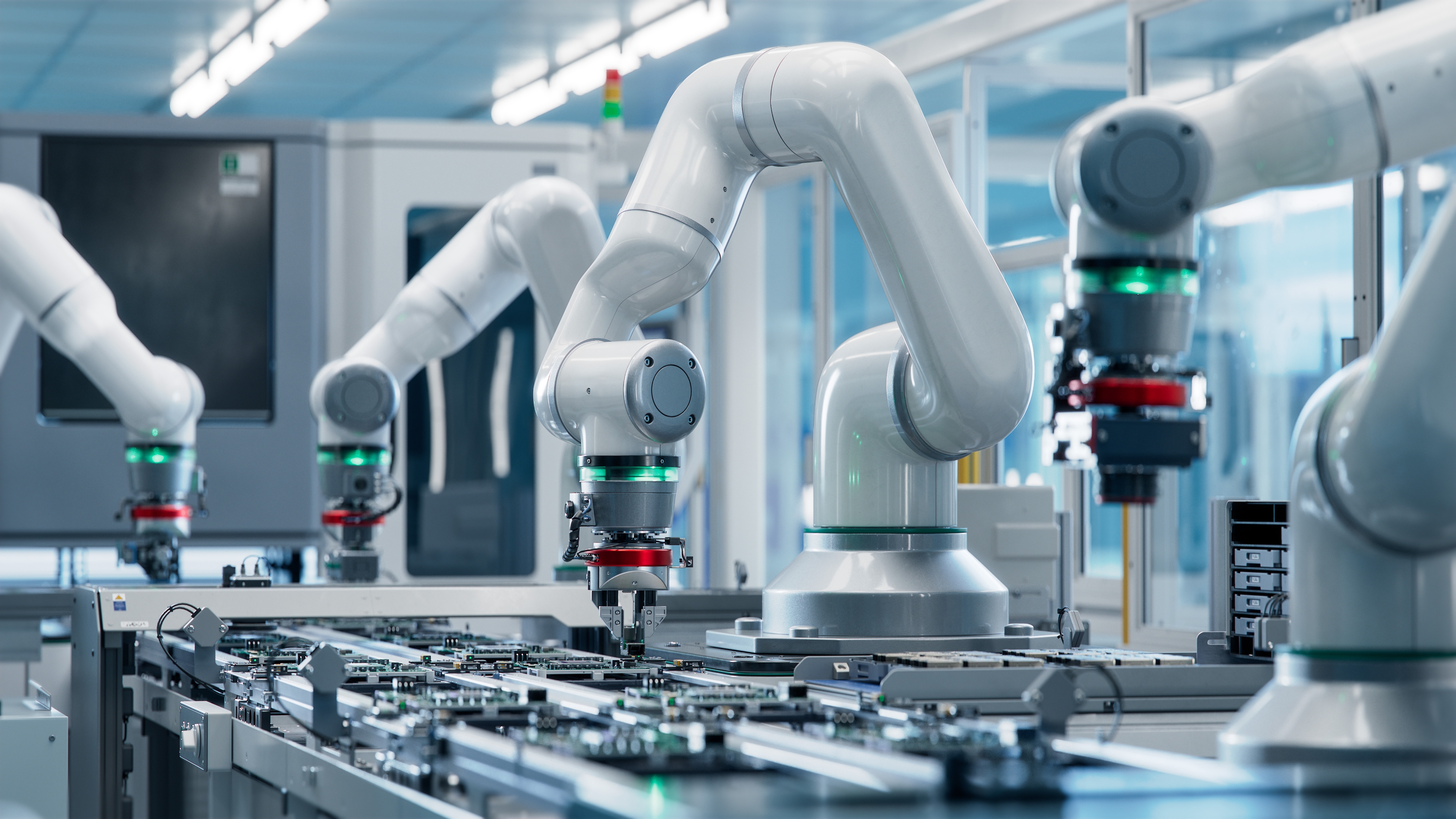
3. Budget: Cost can be a determining factor when choosing an industrial or collaborative robot;
4. Productivity: The efficiency and productivity of the robot are factors that must be considered. Industrial robots are faster and more accurate in performing repetitive tasks. Collaborative robots, on the other hand, can be more flexible and adaptable, which can lead to higher productivity in tasks that require human interaction.
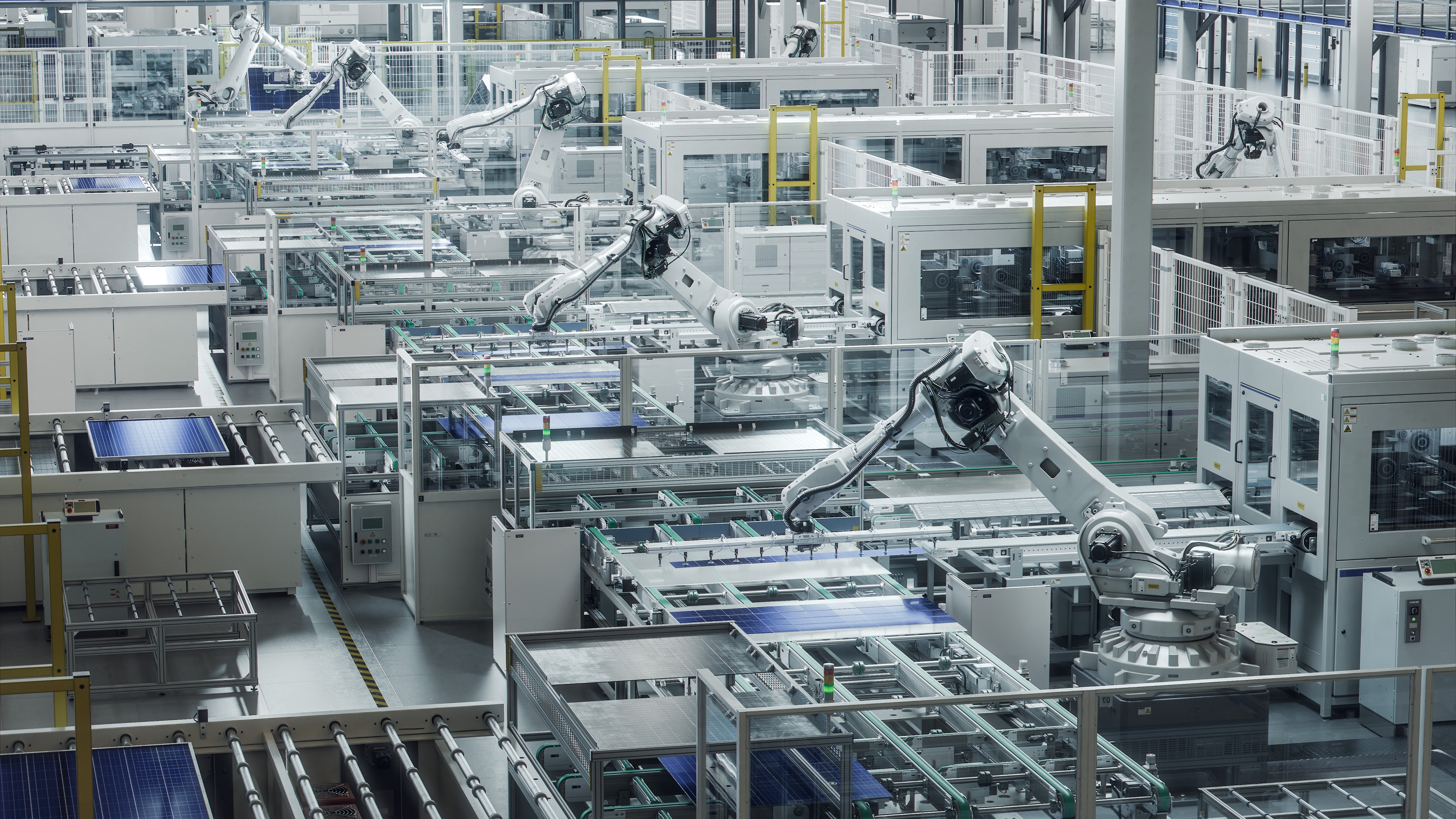
By considering these factors, it becomes easier to choose the most suitable option for each industry. At ESI we develop customized industrial solutions, tailored to the specific needs of each customer. Thus, we evaluate all parameters, understand the main needs and help our customers decide between industrial and collaborative robots.
SEE ALSO: Industrial Robotics: One of the Pillars of Industry 4.0
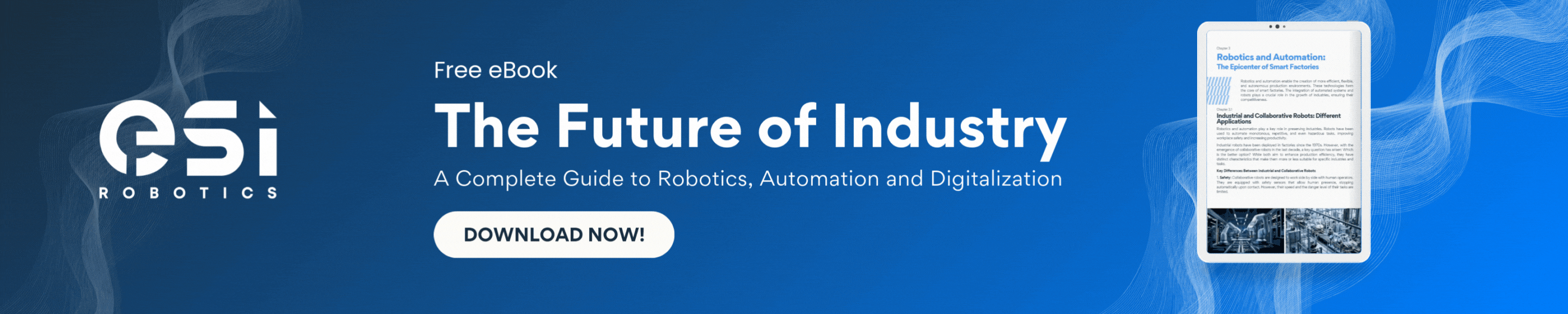