Corex, a company specialized in manufacturing tubes and corner protectors, presented ESI Robotics with a challenge: to automate the palletization process of cardboard tubes, which had been exclusively manual until then. We eagerly embraced this challenge and developed a robotic cell capable of performing this process precisely and efficiently!
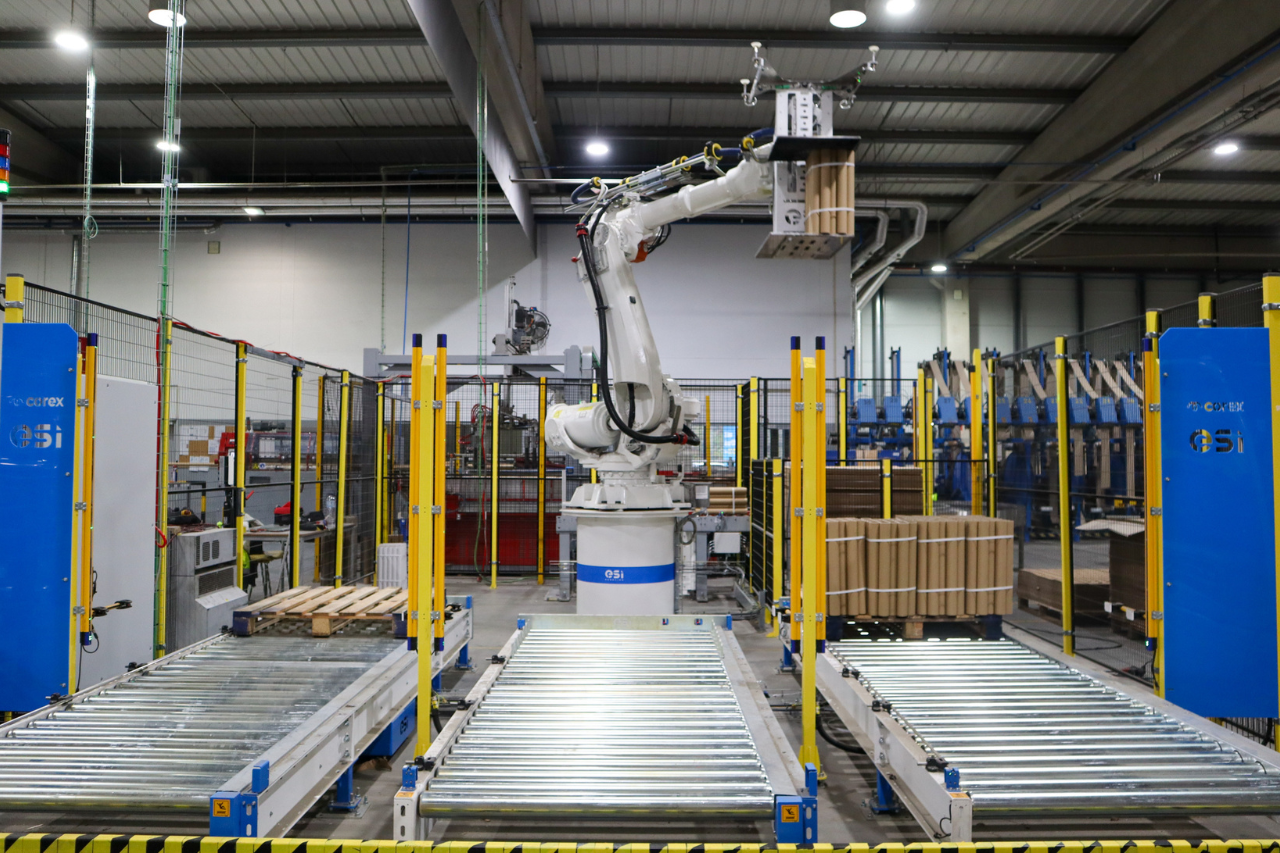
Manual palletization required intense physical effort, as it involved repetitive movements and handling heavy loads. This posed ergonomic risks for workers, increasing the likelihood of injuries and medical leave. Additionally, the company faced difficulties in finding labor, which limited productivity growth and compromised order fulfillment.

ESI Robotics developed a pioneering solution—a robotic cell for cardboard tube palletization, designed to meet Corex’s specific production needs while ensuring precision, repeatability, and efficiency.
The cell can handle different tube sizes and references, performing palletization in a vertical or horizontal position at three possible palletizing points. Additionally, the robot, using the vacuum system on the gripper, can place interlayers between multiple product layers. Once the tube size and reference are set, the robot's gripper automatically adjusts.
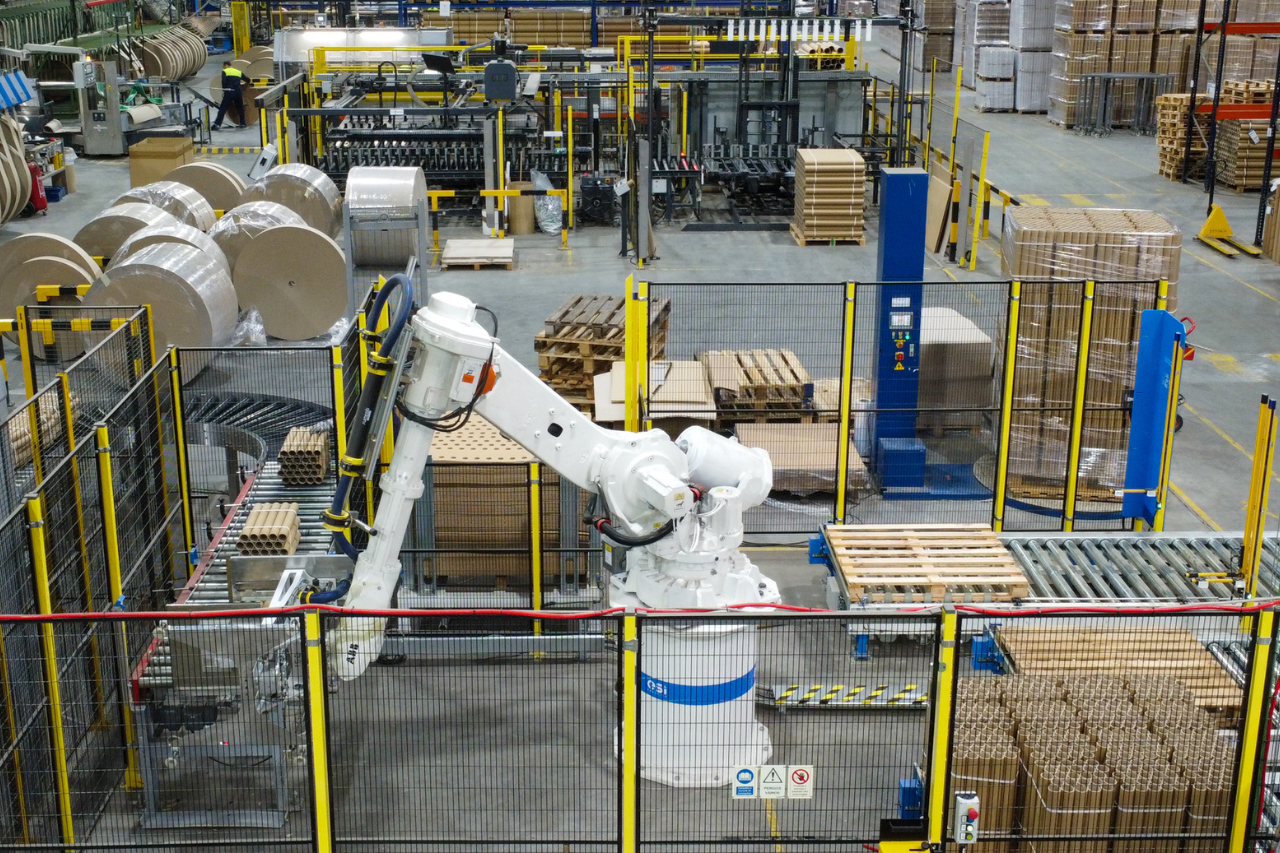
Project Results: Impact on Production and Sustainability
The implementation of this robotic cell brought significant benefits to our client:
- Increased productivity: Corex can now handle a higher volume of orders without compromising deadlines;
- Improved working conditions and worker safety: Reduced physical strain and lower risk of operator injuries;
- Reduced environmental impact: Process optimization minimized errors and, consequently, material waste, contributing to lower environmental impact;
- Greater operational autonomy: By leveraging automation and robotics, Corex successfully overcame the challenges posed by labor shortages, ensuring a stable and predictable production flow.
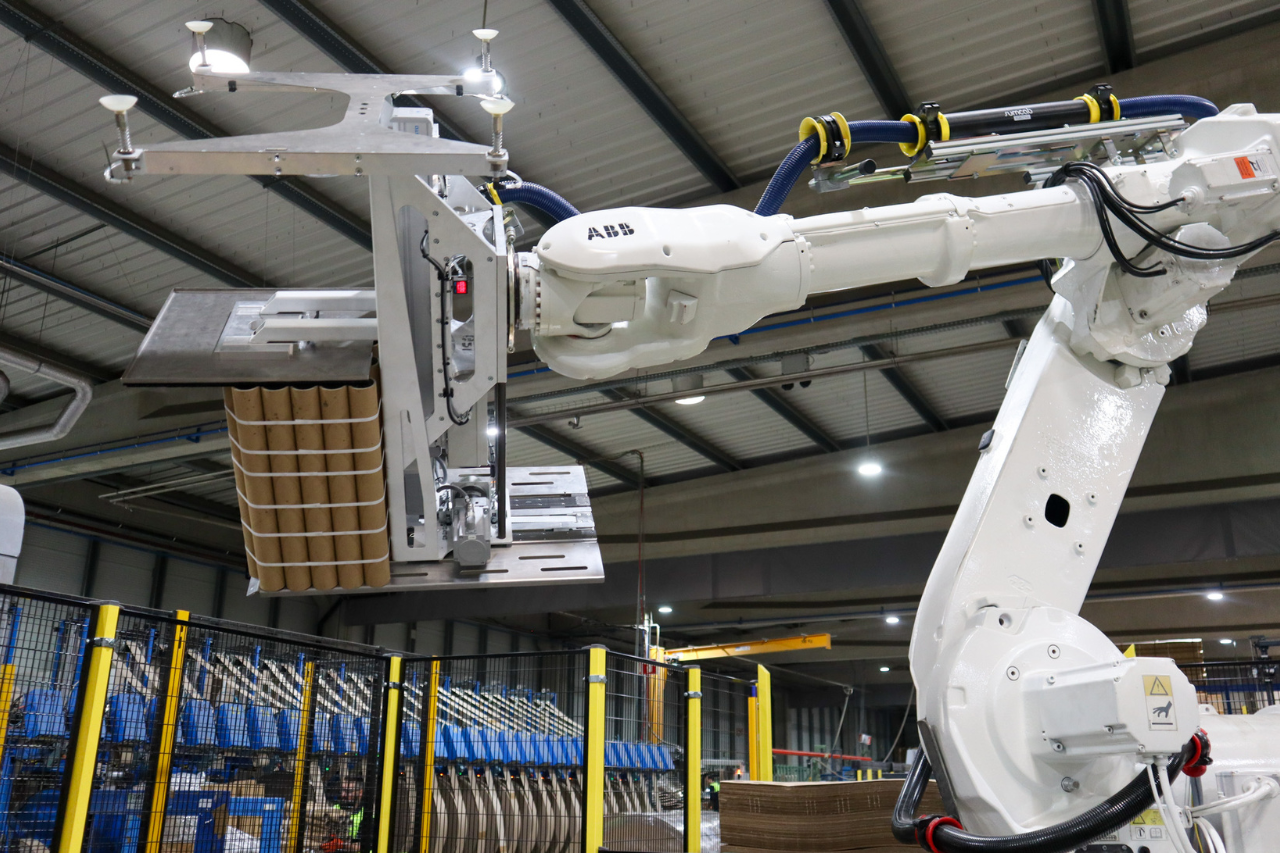
The implementation of this robotic cell was a resounding success, proving that innovation is the key to overcoming challenges and boosting productivity! In summary, the solution developed by ESI Robotics delivered clear improvements in efficiency, safety, and quality.
Is your company ready to take the next step?
Talk to us!
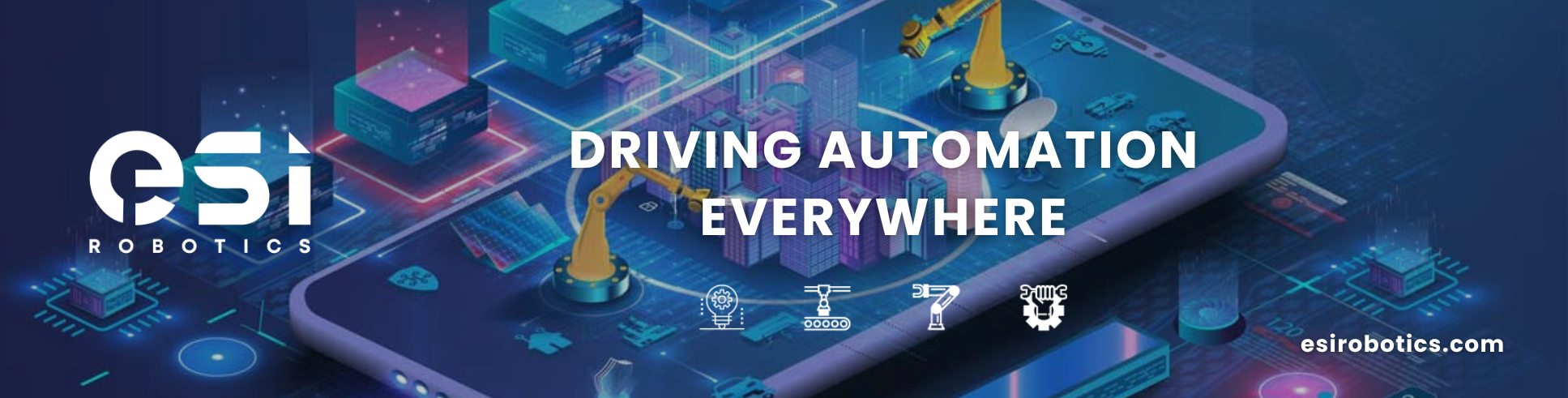