We are witnessing, in the front row, the Fourth Industrial Revolution, often referred to as Industry 4.0. The emergence of different technologies such as artificial intelligence, robotics, the Internet of Things (IoT), or the Industrial Internet of Things (IIoT) has transformed production processes and introduced the concept of the smart factory!
An automated production system or smart factory allows you to efficiently manage employee absences while providing the flexibility to quickly adapt to sudden variations in demand or, if necessary, to move into the production of new products.
After experiencing an atypical pandemic, the importance and potential of smart factories are evident.
SIX PRINCIPLES OF INDUSTRY 4.0
- Interoperability: cyber-physical systems (part support, assembly stations and products), humans and Intelligent Factories connect and communicate with each other via the Internet and Cloud Computing.
- Virtualization: a virtual copy of the Smart Factories is created by interconnecting data sensors (that monitor physical processes) with virtual plant models and simulation models.
- Decentralization: the ability of the cyber-physical systems of the Smart Factories to make decisions without human intervention.
- Real-Time Capability: the ability to collect and analyze data and deliver knowledge derived from these analyses immediately.
- Service-Oriented: the delivery of services (from cyber-physical systems, humans, or Intelligent Industries) via Cloud Computing.
- Modularity: flexibly adapting Smart Factories to changing requirements by replacing or expanding individual modules.
SMART FACTORIES: WHAT DOES IT MEAN?
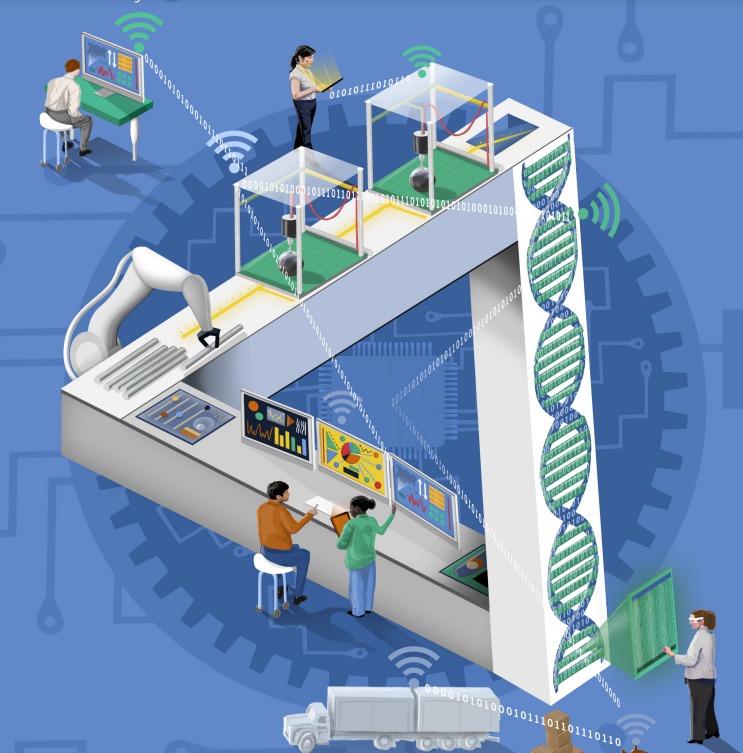
In "The smart factory" report, Deloitte highlights five key aspects of smart factories:
- Connectivity: smart factories require processes to be connected to generate up-to-date data, central to making informed, real-time decisions. This data integration enables a complete view of processes, driving informed decision-making.
- Optimization: A smart factory allows operations to be run with minimal manual intervention, based on exceptionally reliable, automated workflows.
- Transparency: Access to updated data in real-time allows greater visibility of the entire process, enabling informed decisions to be made.
- Proactivity: in a proactive system, employees and systems can predict and act before anomalies appear.
- Flexibility: A smart factory has the flexibility to adapt to changes with minimal intervention and impact.
How to be part of the Smart Factory era?
Transitioning to a smart factory is not an overnight process. The first step will be to draw up a comprehensive strategy that aggregates the entire organization.
To manage a smart factory, it is fundamental to think about optimizing processes and consider an integrated solution that increases productivity and reduces costs. The unique solutions developed by ESI ensure the highest value and performance for your industry.
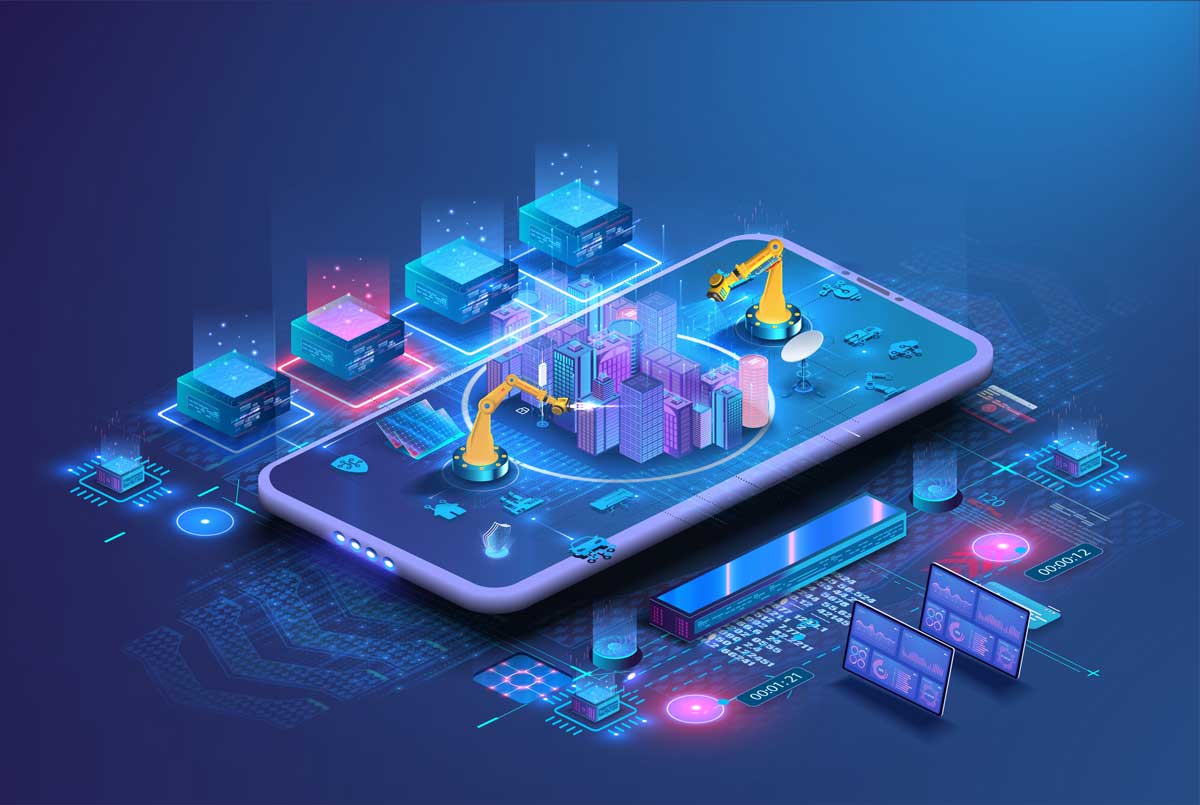
SEE ALSO: Industrial Robotics: One of the Pillars of Industry 4.0